Sweet dreams are made of recycled materials
The lonely mattress propped up against a tree on the kerbside is a familiar sight on our neighbourhood streets.
In fact, Australians throw away about 1.8 million mattresses and over 500,000 bed bases a year, with a high percentage ending up in landfill.
Sustainability Victoria is here to make a change, investing in research that could produce a bed made from recycled plastic that is also recyclable at the end of its life.
A $300,000 Victorian Government grant delivered by Sustainability Victoria has enabled Swinburne University to partner with start-up Robovoid and GT Recycling to explore innovative ways to use recycled plastics in bed bases and mattresses.
Robovoid’s Dr John Stehle explains that the mix of materials present in traditional bedding makes recycling difficult, both practically and economically, so the majority of our unwanted bed bases and mattresses get sent to landfill.
“Recycling companies don’t like recycling bedding because it’s big and cumbersome to handle, but it also has a combination of materials which is hard to dissect,” John says.
“In each traditional bed base, you’ve got a lot of timber and about 1,000 staples. No one wants to pull out all those staples so they can use the timber again.
“And in the mattress, you've typically got metal springs, foam and various other materials. While the springs can be extracted and sold as scrap metal, and some foams can be used for carpet underlay, most materials have little value and invariably end up in landfill.”
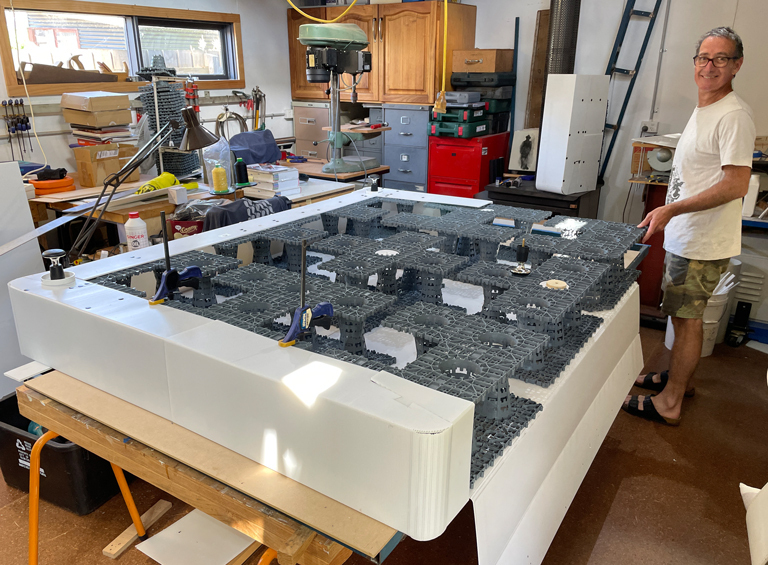
Enter ROBOBED. We’ve all heard of beds filled with water. What about beds made of plastic?
Robovoid had already developed recycled plastic products for concrete applications. Discussions with researcher Tracey Pryor from the Australian Bedding Stewardship Council sparked the idea of producing a bed using the same materials.
“One of the reasons we’re using plastic in this project is because it’s so useful,” John says.
“You can mould it into different shapes, it's cost effective and it's light. Our bed base is much lighter than a timber bed base.
“With a traditional bed base, the timber normally comes from a forest, so we're avoiding the need to cut down plantations or increase deforestation.
“The springs in a traditional mattress are made from steel and normally the steel is a virgin material steel. So again, we are trying to replace that with a recycled product and create a more circular bed solution.”
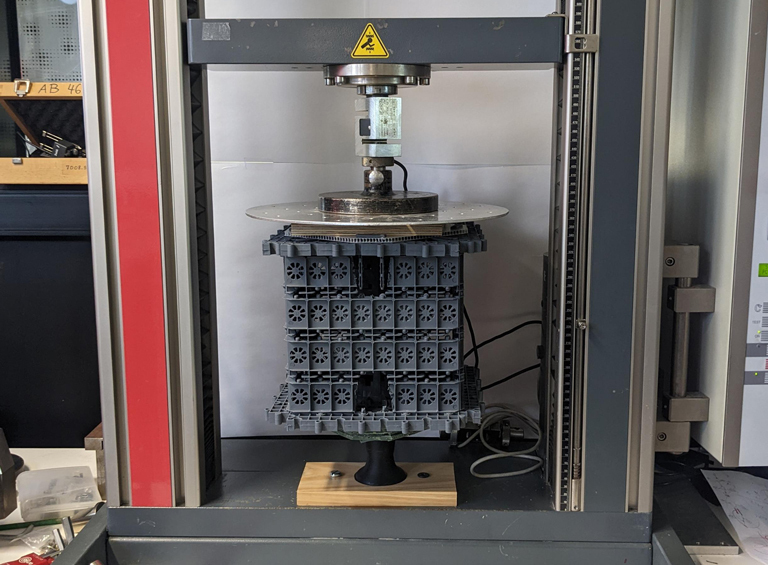
GT Recycling’s Doug McLean agrees, saying there’s also a lot of recycled plastic available.
“There's so much of it that we need new products to be developed to use up all the recycled plastic, otherwise it just sits in warehouses or goes to landfill,” Doug says.
Swinburne University’s Dr Mostafa Nikzad explains that designing for recyclability is uncommon.
"It's certainly an approach we are adopting here, to ensure that what comes together in the end can be easily recycled when it's time to buy a new bed."
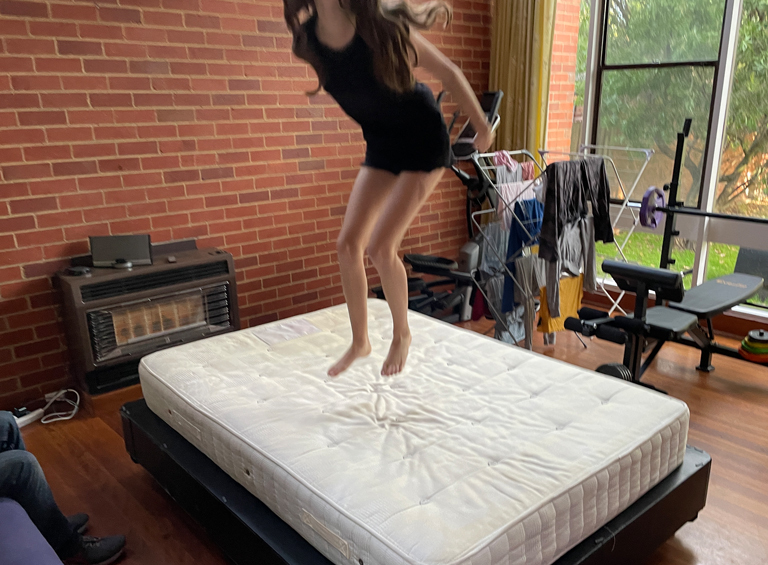
Six months into product development, the team is already seeing success.
Starting with the bed base, GT Recycling has supplied the recycled plastic feedstock and Robovoid has optimised the final base design to meet performance requirements.
Swinburne has undertaken rigorous testing to understand the variabilities and uncertainties that come with using recycled materials and how they can be best integrated with the Robovoid design to ensure the right prototype performance.
“Initially, my daughter was jumping up and down on the base. That was okay, but now it's strong enough for me to jump up and down on. So we think that's a pretty good test!,” John says.
“We've also done some testing with Australian bedding manufacturer A H Beard. We sent one bed up to Sydney and then they put a big 120 kg roller on it to test performance.”
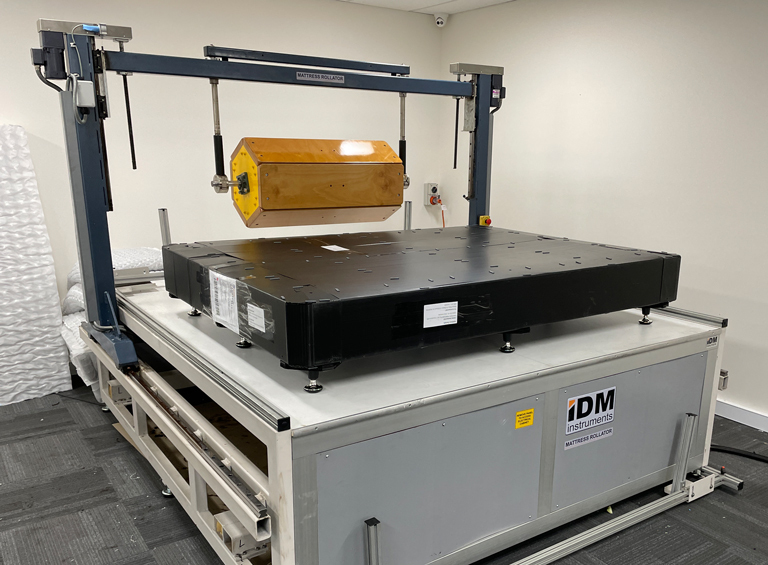
Producing the mattress is a different proposition. Australians have a variety of comfort preferences, with most opting for a ‘medium’ to ‘firm’ mattress.
“The mattress is a lot more challenging than the bed base mainly because of the dynamic performance requirements,” John explains.
“We're actually making a new injection moulded product for that and we hope to start producing mattresses by the end of this year.”
Mostafa says the support from Sustainability Victoria has been crucial to bringing this project to life.
“Broadly, this sort of activity is very important because it imparts confidence that if you marry up the right set of skills from academia and industry, it's possible to design functional products with recycled materials.
“So this project has been an important step to show that yes, you can do it.”