Martogg finds circular solution for plastic bottles
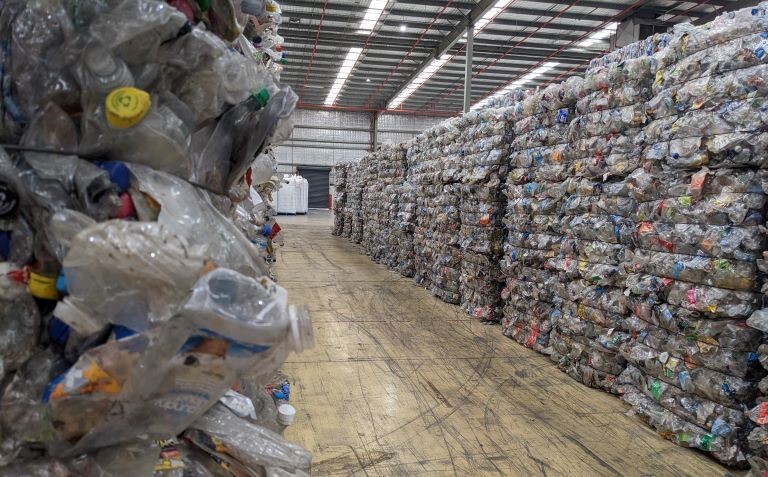
Plastic recycler Martogg is transforming bottles from our recycling bins into clean, food-grade plastic that can be reused.
With support from the Victorian Circular Economy Recycling Modernisation Fund, Martogg has invested in new technology to identify and sort different bottles, grind them into plastic flakes and thoroughly wash them, resulting in recycled plastic that is 99.5% pure.
In theory, many commonly used plastic items can be recycled. But it takes cutting-edge technology to recycle plastics for reuse in food and drink packaging due to strict safety requirements.
Martogg’s Heath Boucher says it’s a project they’ve been exploring for a number of years.
“The business is already passionate about recycling in general, but it’s exciting for us to be recycling Australian waste and creating products for Australia,” Heath says.
“Technology like this does exist in Australia, but not to this level which means we can accept a wider variety of plastic.”
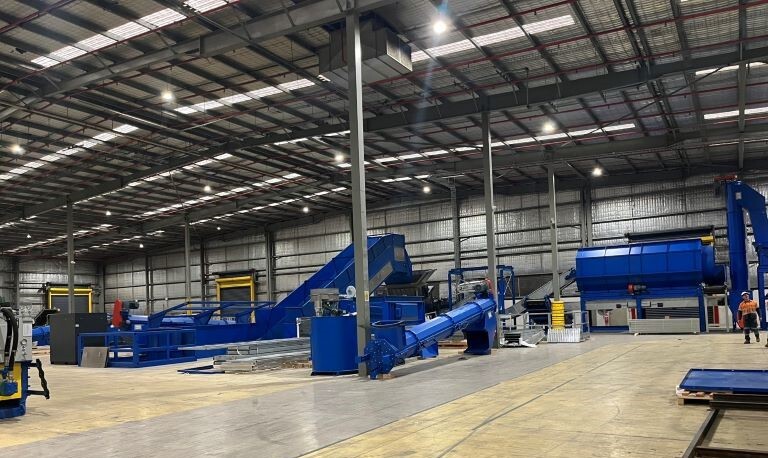
The process
The process to transform used bottles into clean, food-grade plastic is complex:
- First, a forklift places large loads of plastic recycling onto a conveyer belt.
- After going through a bale breaker to separate the load, a ferrous magnet pulls out any metal from the load.
- A trommel or screen then divides undersized and oversized items, together with bottle lids, dirt and sand.
- Next, an eddy current pulls out any aluminium cans which are collected for recycling.
- A mechanical de-labeller removes any labels before the bottles are presented to five optical sorters.
- Through the power of French AI, the sorters identify the type and shape of the bottle, using air nodules to push the correct bottles to the next stage.
- After the optical sorting, the bottles head into a friction washer to remove any glass fibres that may have been present in the recycling load.
- Then the bottles are ground up into plastic flakes.
- The flakes progress through two stages of hot, caustic washing to ensure they are clean. The wash is heated to 85 degrees and the pH level is set at 12 to remove any adhesive or other impurities.
- After drying, the flakes are rinsed with fresh water to remove any process waters.
- The clean flakes are de-dusted before going through another optical sorter which guarantees 99.5% food-grade quality plastic.
From early 2024, works on the plant will be complete and Martogg will be able to start transforming plastic recycling into new products that will appear on our supermarket shelves, like bottles and strawberry punnets.
“From a washing perspective, we’ll be able to get through about 2 tonnes of plastic an hour or around 20,000 tonnes a year,” Heath says.
“And from a sorting perspective, it will be about 4 tonnes an hour or around 40,000 tonnes a year.
“That’s equal to about a billion plastic bottles a year with the current washing capacity. In the second phase of the project, we’ll be matching sorting capacity, so it’ll be about 2 billion bottles a year.”
The funding
This project was funded jointly by the Australian and Victorian Governments through the Victorian Circular Economy Recycling Modernisation Fund. This fund supports projects that improve the quality and quantity of recyclable materials in Victoria by upgrading infrastructure, technology or processing capacity.
The Victorian Government’s funding is a part of its $515 million investment to transform the state’s waste and recycling sector, including $380 million under the government’s circular economy policy Recycling Victoria: a new economy.
The Australian Government is contributing funding as part of its $250 million Recycling Modernisation Fund (RMF). The RMF is accelerating Australia’s circular economy so that when a product is no longer useful or required for its initial purpose, it is either reused, recycled or remanufactured.