Building greener homes with recycled plastic
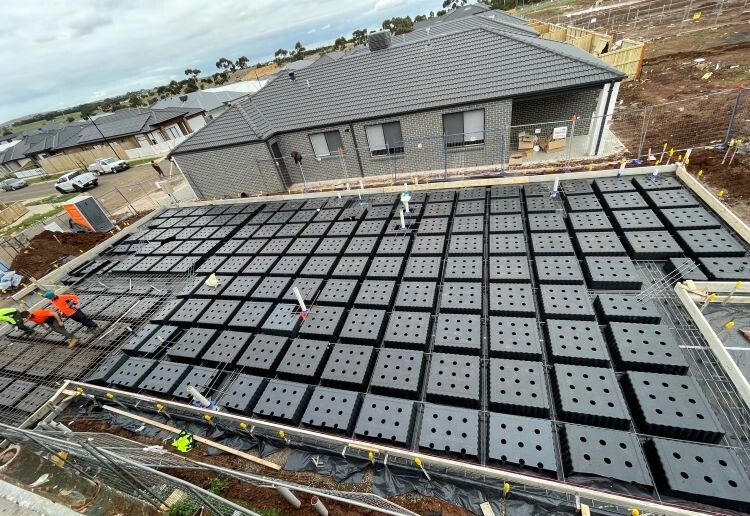
Millions of pieces of polystyrene are polluting Melbourne's Yarra River, leaching chemicals into the water and harming marine life according to ABC News.
The majority of this pollution comes from the construction industry where polystyrene is used in “waffle pod” form to fill concrete slabs in residential housing.
A report by the Yarra Riverkeeper Association found that of 80 construction sites within the Yarra River catchment area, 98 per cent of them had polystyrene pollution either on site or in the drains nearby.
What if there was an alternative?
Plastic injection moulding manufacturer Socobell has teamed up with CLEVACO® to produce a more environmentally-friendly solution to polystyrene waffle pods.
Socobell’s project engineer David Paizis says the CLEVA POD® is a like-for-like replacement for traditional polystyrene used in housing construction meeting the Australian Standard AS 2870, but it’s made from recycled plastic.
“Polystyrene makes a mess and is really bad for the environment,” David says. “It also contaminates the concrete, so when they go to demolish a house and separate all the building materials, they can’t recycle the concrete.
“By using recycled plastic to manufacture the CLEVA POD®, we’re not creating new plastic and we’re diverting waste from landfill at the same time. On top of that, the plastic pods can be separated quite easily from concrete in demolition, so both materials can be recycled.”
This ability to recover, recycle and reuse the plastic pods at the end of its life contributes significantly towards a circular economy.
CLEVA POD®s also mean savings for the construction industry, with the product taking much less time to install and being more economical to transport.
“Polystyrene pods for one house typically take up a full truckload,” says David. “With the CLEVA POD®, you could fit enough product for 10 houses on a truck the same size.”
This also reduces the carbon associated with transport.
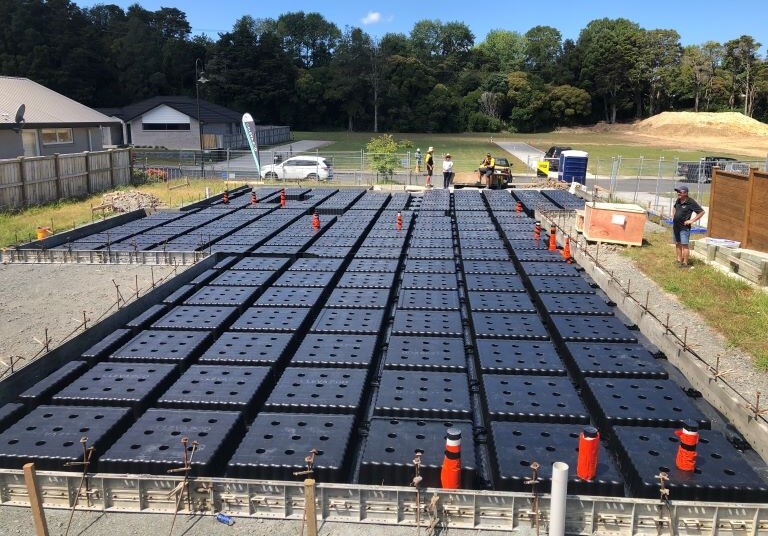
The process
Supported by a grant from Sustainability Victoria’s Recycling Modernisation Fund delivered on behalf of the Victorian Government, Socobell was able to invest in a new machine capable of moulding a product of this size.
The injection moulding process takes a recycled plastic bead and feeds it through a hot barrel, which melts the material and forces it together. Once melted to the right temperature, the material is pushed into a mould to form the CLEVA POD®.
David says Socobell is currently manufacturing small batches of pods to introduce construction companies to the product after successful trials in both Australia and New Zealand.
Once at full capacity, Socobell will be able to divert 2,000 tonnes of plastic per year, with plans to expand to a second machine as demand increases.
“There’s a lot of interest in this product,” David says.
“A lot of concrete and steel manufacturers are looking to clean up their act and get away from polystyrene products.
“Once they get their heads around CLEVA POD®, we’ll be looking to increase our manufacturing capacity, divert even more waste from landfill, and put Socobell on the map for being a green plastic manufacturer.”
Supporting projects that improve recycling
This project was funded jointly by the Australian and Victorian Governments through the Victorian Circular Economy Recycling Modernisation Fund. This fund supports projects that improve the quality and quantity of recyclable materials in Victoria by upgrading infrastructure, technology or processing capacity.
The Victorian Government’s funding is a part of its $515 million investment to transform the state’s waste and recycling sector, including $380 million under the government’s circular economy policy Recycling Victoria: a new economy.
The Australian Government is contributing funding as part of its $250 million Recycling Modernisation Fund (RMF). The RMF is accelerating Australia’s circular economy so that when a product is no longer useful or required for its initial purpose, it is either reused, recycled or remanufactured.