Reduce boiler, steam and process heating costs in your business
Your boiler, steam and process heating work together. They should be treated as one system.
When your boiler, steam and process heating isn’t working together efficiently, they can add up to 60% to your energy bill.
But there are ways you can reduce the amount of energy you use in the process, which can:
- lower your gas bill
- cut your maintenance costs
- decrease your greenhouse gas emissions
- improve safety and work conditions for your employees.
The figures on this page come from our Boosting Business Productivity program. We worked with more than 300 businesses to explore their energy use and minimise their energy cost.
Assess your current energy use
Install a gas meter to your system to track and monitor its use. This data can be analysed to identify opportunities to save energy. If you have an engineer on staff, they’ll be able to analyse the data for you. Otherwise, find out more about gas measurement and monitoring.
Every business is different. The best way to get a clear idea of what’s using the most energy in your business is by getting an energy audit. An energy auditor can review your energy bills and the way your business operates, to identify where you’re losing energy and what you can do about it.
Find an energy auditor near you.
It’s always good to seek advice and knowledge from similar businesses and industry groups.
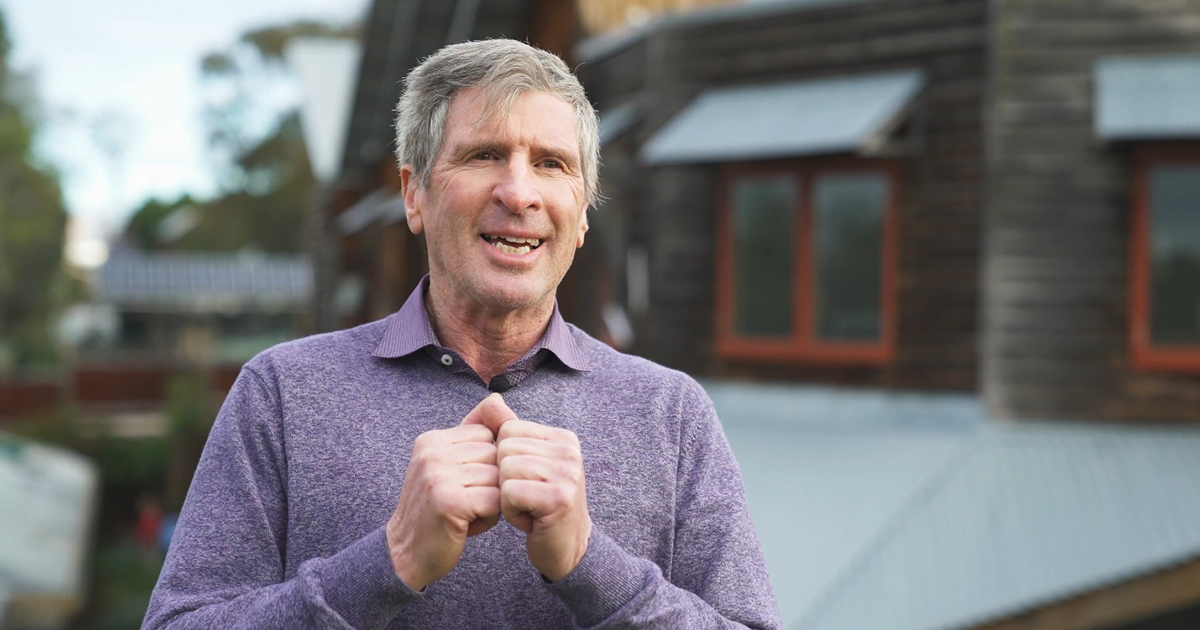
Meet David. After upgrading processes and equipment at his dessert-making business, he saw significant energy savings.
Ways to reduce boiler, steam and process heating costs
1. Implement heat recovery
Heat recovery is a process where you redirect and use heat that would otherwise be vented outside, to preheat the boiler feed water.
Implement condensate recovery, a process where you redirect condensate into your boiler feed water tank.
To get the most out of your boiler, regularly blowdown water using steam pressure to remove any build-up of impurities, which improves the efficiency of the system.
Benefits
On average, heat recovery will:
- cost less than $70,000 to implement
- save nearly $45,000 annually
- take less than 2 years to pay back
- save nearly 400 tonnes of greenhouse gas emissions annually.
2. Add operational controls and a variable speed drive to your system
Operational controls and variable speed drives work together to make your system more efficient.
Operational controls can switch the system on or off and adjust the temperature according to demand.
A variable speed drive adjusts the speed of combustion air fans and feed water pumps.
Benefits
On average, adding operational controls and variable speed drive will:
- cost less than $27,000 to implement
- save more than $50,000 annually
- take less than 1.5 years to pay back
- save more than 270 tonnes of greenhouse gas emissions annually.
3. Insulate piping
Insulate steam, hot water and condensate piping to reduce heat loss and improve productivity of the system.
Benefits
On average, insulating piping will:
- cost less than $16,500 to implement
- save more than $7500 annually
- take 2 years to pay back
- save more than 45 tonnes of greenhouse gas emissions annually.
4. Regular maintenance
Schedule regularly maintenance with a technician to make sure your system is working efficiently.
Regularly check for:
- burner combustion efficiency
- steam leaks
- heat losses
- faulty steam traps.
This can save up to 5% of your energy bill.
Benefits
On average, annual regular maintenance will:
- cost less than $23,500
- save more than $51,500
- take less than 1 year to pay back
- save more than 270 tonnes of greenhouse gas emissions.
5. Measure and assess the performance of your system
Install electricity and gas meters to your boiler, steam and process heating system to monitor use.
The metre can show you how much energy the system uses and when. This data can be analysed to see if it’s working efficiently or when it’s not.
An operations manager will be able to analyse the data for you. If you don’t have an operations manager, call a technician.
Benefits
On average, measuring, analysing and updating the system will:
- cost less than $50,000
- save more than $18,000 annually
- take less than 3 years to pay back
- save more than 160 tonnes of greenhouse gas emissions annually.
For more information about using your boiler, steam and process heat efficiently, watch our gas video series.
What else can you do?
Upgrade your boiler, steam and process heating system at a discount
You may be eligible for discounted energy-efficiency products and services, including boiler, steam and process heating, through the Victorian Energy Upgrade program.
To get started, contact an accredited provider.