Big savings for Foamex after investing in energy efficiency
Upgrading equipment and improving manufacturing processes has cut gas costs by 17% and 23% at Foamex’s Bayswater and Somerton facilities.
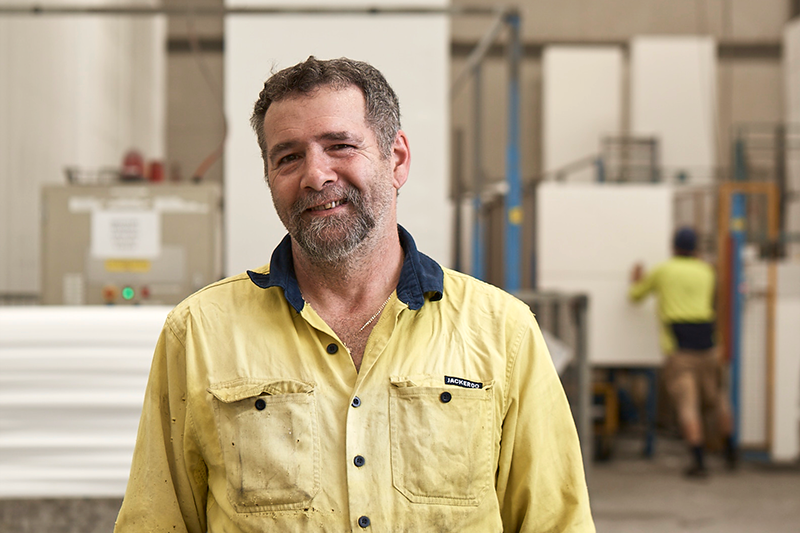
Foamex has been supplying polystyrene products to the Australian market since 1982. In recent years, the business has seen a significant increase in energy costs at their two Victorian sites.
“We use a lot of gas to heat water in our boilers,” explained Tony Katsigiannis, Group Manufacturing Manager. “It’s our biggest production cost in manufacturing polystyrene and we’ve been hit hard by rising gas prices.”
In 2014, the business invested in more efficient boilers and improved the steam condensate return systems. “This was really successful, and it spurred us on to find more ways to tackle rising gas prices.”
They applied for an energy assessment grant to bring in an external energy expert who could look at their manufacturing processes and show them how to find more savings. The cost of the energy audit was around $20,000 for each site.
After completing several of the energy upgrades recommended in the audit report, they saved around $100,000 a year with:
- 17% reduction in gas energy costs at their Bayswater site
- about 23% reduction at the Somerton facility.
Make the most of what you already have
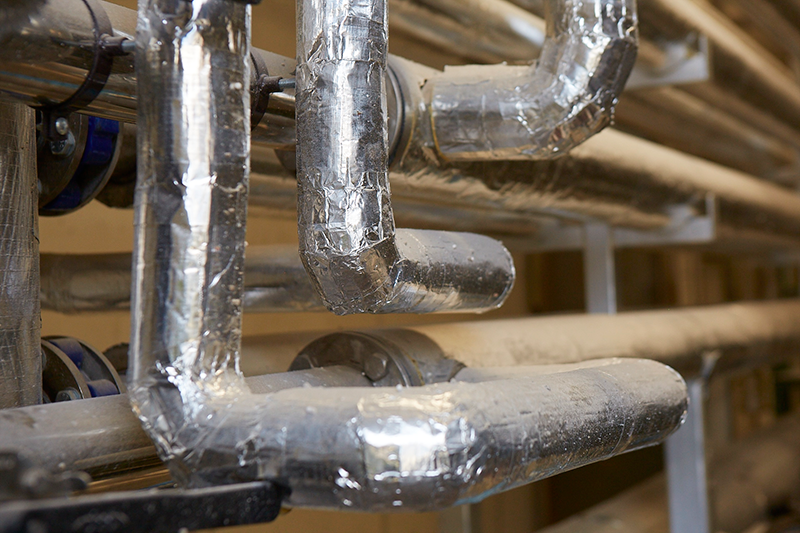
The biggest gas saving came from re-using the steam already generated during the manufacturing process.
“We installed new equipment to capture steam coming from the bigger pieces of plant equipment. We use this steam to pre-heat the water going into the boilers,” explained Tony. “We can get the feedwater temperature up by as much as 25ºC, which means we need way less gas to heat the water in the boilers.”
Other upgrades included replacing two defective steam traps and installing some extra traps. These traps act as a valve that filters out condensed steam and non-condensable gases such as air without letting steam escape.
At the Somerton plant, the company installed new filter packs in the cooling tower so it would operate more effectively. The cooling tower is used to cool condensate return water from the manufacturing process and supply water feed to vacuum pumps.
Equipment upgrades pay for themselves
Doing your energy efficiency research before investing can help you make upgrade choices that pay for themselves over time.
“We spent a bit on the upgrades,” Tony said. “The total cost was $125,000 and that was with using our own labour to keep costs down. But we covered $50,000 with a gas efficiency grant from SV, so we’ve covered our costs in well under a year.
“Now we get to reap the benefits of ongoing energy savings.”
Multiply the impact of energy savings
Foamex are now looking to make similar upgrades at a recently acquired Victorian site and their South Australian site.
“I’d recommend an energy audit to any business,” Tony said. “It helps you see where the opportunities for savings are and gives you a good basis to get started.”